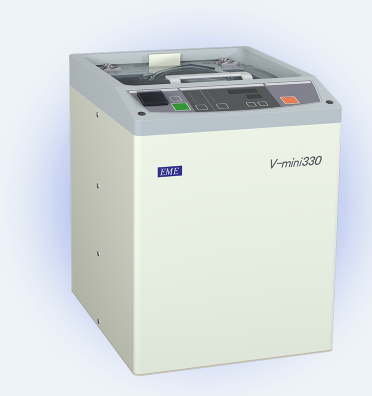
真空攪拌消泡混合器在電子設備密封材料處理中起著關鍵作用,能有效提升材料性能與可靠性,如密封性、粘合性等。對于 V - MINI330 真空攪拌消泡混合器,在不同類型電子設備密封材料處理時,其技術參數會因材料特性與設備需求不同而有所差異。以下將從不同方面闡述這些差異:
攪拌速度
對于高粘度密封材料:像部分用于芯片封裝的有機硅密封膠,這類材料流動性差,氣泡排出困難。V - MINI330 需較高攪拌速度,以增強剪切力,打破氣泡與材料間作用力,促使氣泡快速上升排出。如在處理此類高粘度材料時,攪拌速度可能需達到 1000 - 1500 轉 / 分鐘,才能實現高效消泡與均勻分散。若速度過低,氣泡難以從材料內部脫離,影響密封材料性能,導致密封效果不佳,水汽等易侵入電子設備,縮短使用壽命2。
對于低粘度密封材料:如某些用于顯示屏密封的膠水,其流動性好,但氣泡易在攪拌過程中重新混入。此時 V - MINI330 攪拌速度不宜過高,一般控制在 300 - 500 轉 / 分鐘,避免因高速攪拌產生過多新氣泡。較低速度既能保證材料均勻混合,又能防止過度攪拌引入氣泡,確保密封材料的光學性能與粘合性能不受影響,維持顯示屏的顯示效果與可靠性2。
真空度
對易揮發成分的密封材料:部分含揮發性有機溶劑的密封材料,在處理時需精準控制真空度。若真空度過高,溶劑快速揮發,可能改變材料成分比例,影響密封性能。如在處理此類材料時,真空度通常控制在 - 0.06MPa 至 - 0.08MPa 之間,既保證氣泡有效排出,又避免溶劑過度揮發。以某款含特殊添加劑的密封膠為例,真空度過高會使添加劑揮發,降低密封膠的耐老化性能,影響電子設備長期穩定性2。
對無易揮發成分的密封材料:對于大多數不含易揮發成分的密封材料,可適當提高真空度以增強消泡效果。如在處理一些環氧基密封材料時,真空度可提升至 - 0.09MPa 至 - 0.095MPa,加快氣泡逸出速度,減少材料內部殘留氣泡,提高密封材料的致密性與絕緣性能,保障電子設備在電氣性能方面的穩定性2。
攪拌時間
對于復雜成分密封材料:如用于多層電路板密封的復合材料,其成分復雜,包含多種填充劑、固化劑等。為使各成分均勻分散,V - MINI330 需較長攪拌時間,可能在 15 - 30 分鐘之間。足夠的攪拌時間能確保各成分充分混合,發揮協同作用,提升密封材料的綜合性能,保證電路板在復雜環境下的可靠性。若攪拌時間不足,成分分散不均,會導致密封材料局部性能差異,影響電路板整體密封效果2。
對于簡單成分密封材料:像一些單一成分的密封油脂,用于小型電子元件的防潮密封,其成分簡單,混合相對容易。攪拌時間可縮短至 5 - 10 分鐘,既能實現氣泡排出與材料均勻化,又能提高生產效率。若攪拌時間過長,可能對材料性能產生負面影響,如使密封油脂的粘性降低,影響其對電子元件的附著性2。
溫度控制
對溫度敏感密封材料:部分用于光學電子設備的密封材料,對溫度極為敏感。如某些含特殊光學添加劑的密封膠,溫度過高會導致添加劑分解,影響材料光學性能。V - MINI330 在處理這類材料時,需嚴格控制溫度在 20 - 25℃之間,通過冷卻系統或加熱系統維持穩定溫度,確保密封材料性能不受溫度影響,保障光學電子設備的成像質量與光學穩定性2。
對普通溫度耐受性密封材料:對于大多數普通電子設備的密封材料,溫度耐受性較好。在處理過程中,溫度控制相對寬松,一般在室溫(25 - 30℃)下即可進行攪拌消泡處理。但在一些特殊工藝要求下,如加速某些密封材料的固化反應,可能會適當提高溫度至 40 - 50℃,利用 V - MINI330 的溫度調節功能,控制溫度以滿足材料處理需求,提高生產效率2。
2
用真空攪拌消泡混合器將電子器件應用于電子產品中山 幸弘
V - MINI330 真空攪拌消泡混合器在提升燃料電池材料性能方面的具體工藝優化
在燃料電池材料的制備過程中,材料內部存在的氣泡會對其性能產生諸多不利影響,如降低材料的導電性、熱傳遞效率以及影響其結構穩定性等。而 V - MINI330 真空攪拌消泡混合器在提升燃料電池材料性能方面具有重要作用,以下從多個方面闡述其具體工藝優化:
真空環境設定優化
真空度精準控制:通過精確調節 V - MINI330 真空攪拌消泡混合器內的真空度,可有效改變材料內部氣泡所受壓力。在燃料電池材料制備時,不同的材料體系對真空度要求存在差異。例如,對于某些含有易揮發成分的燃料電池電極材料,過高的真空度可能導致成分揮發損失,影響材料的化學組成和性能;而過低的真空度則無法充分去除氣泡。因此,需依據材料特性,精準設定真空度,通常可將真空度控制在特定范圍,如 - 0.08MPa 至 -0.095MPa 之間,以確保既能有效破除氣泡,又不影響材料成分2。
真空保持時間優化:合理設置真空保持時間對于去除燃料電池材料中的氣泡至關重要。較短的真空保持時間可能使氣泡無法充分逸出,而過長的時間則會降低生產效率。在實際工藝中,針對不同的燃料電池材料,需通過實驗確定最佳真空保持時間。比如對于質子交換膜燃料電池的催化劑層材料,經過多次實驗驗證,在特定真空度下,保持 15 - 25 分鐘,可使材料中的氣泡含量降低至較低水平,顯著提升材料的均勻性和性能。
攪拌參數優化
攪拌速度調控:V - MINI330 具備可調節的攪拌速度,這對于燃料電池材料的分散和消泡極為關鍵。在材料混合初期,較低的攪拌速度有助于各組分初步均勻分布,避免因速度過快導致某些成分飛濺或團聚。而在消泡階段,適當提高攪拌速度可增強流體的湍動程度,促使氣泡破碎并加速其上升逸出。例如,在制備固體氧化物燃料電池的復合電解質材料時,開始攪拌速度設定為 200 - 300 轉 / 分鐘,待各組分初步混合均勻后,將速度提升至 800 - 1200 轉 / 分鐘進行消泡處理,能有效提升材料的致密度和離子傳導性能2。
攪拌槳葉設計與選擇:不同形狀和結構的攪拌槳葉對燃料電池材料的攪拌效果和消泡效率影響顯著。對于高粘度的燃料電池密封材料,選擇具有強剪切力的槳葉,如錨式槳葉或螺帶式槳葉,能夠更好地分散物料,破除其中的氣泡。而對于低粘度的電解質漿料,推進式槳葉或渦輪式槳葉可提供更高效的混合和消泡效果。在實際應用中,需根據燃料電池材料的流變特性,選擇合適的槳葉,并對其尺寸、角度等參數進行優化,以實現最佳的攪拌和消泡效果。
溫度控制優化
溫度對材料性能的影響:溫度在燃料電池材料的制備過程中起著關鍵作用。一方面,適當升高溫度可降低材料的粘度,使氣泡更容易上升逸出,同時也有利于各組分之間的化學反應和擴散,提升材料的均勻性和性能。另一方面,過高的溫度可能導致材料分解、揮發或發生副反應,從而損害材料性能。例如,在制備聚合物電解質膜燃料電池的膜電極組件時,控制溫度在 60 - 80℃之間,可促進催化劑與聚合物電解質的充分結合,同時有效去除氣泡,提高膜電極的性能。
溫度與真空、攪拌協同優化:將溫度控制與真空攪拌消泡工藝相結合,能進一步提升燃料電池材料的性能。在真空攪拌過程中,根據材料的特性和工藝要求,動態調整溫度。例如,在真空度較高的階段,適當降低溫度,以防止材料因減壓而過度揮發;在攪拌速度較高時,適當升高溫度,以增強材料的流動性,提高攪拌和消泡效率。通過這種協同優化,可實現燃料電池材料性能的大化提升。
混合順序優化
合理安排組分添加順序:在使用 V - MINI330 制備燃料電池材料時,各組分的添加順序對材料性能影響較大。例如,在制備燃料電池的陰極催化劑材料時,先將金屬鹽溶液與部分溶劑混合,進行初步攪拌,使金屬離子均勻分散,然后再加入有機配體和其他添加劑,最后加入還原劑進行還原反應。這樣的混合順序有助于控制材料的粒徑和結構,減少氣泡的產生。同時,在添加過程中,要注意添加速度,避免過快添加導致局部濃度過高,形成團聚或包裹氣泡。
分階段混合與消泡:對于復雜的燃料電池材料體系,采用分階段混合與消泡的方法可有效提升材料性能。例如,在制備固體氧化物燃料電池的陽極支撐體材料時,先將陶瓷粉末和部分粘結劑進行預混合和初步消泡,然后再加入金屬粉末和其他添加劑進行二次混合和消泡。通過這種分階段的工藝,可逐步去除不同階段產生的氣泡,提高材料的致密度和機械性能。
在線監測與反饋優化
氣泡含量實時監測:在 V - MINI330 真空攪拌消泡混合過程中,利用光學傳感器、超聲傳感器等技術對燃料電池材料中的氣泡含量進行實時監測。通過實時獲取氣泡的大小、數量和分布信息,可及時調整真空度、攪拌速度等工藝參數,確保材料中的氣泡含量始終處于可控范圍內。例如,當監測到氣泡含量超過設定閾值時,自動提高攪拌速度或延長真空保持時間,以增強消泡效果。
材料性能實時反饋:除了監測氣泡含量,還可通過在線檢測材料的電導率、熱導率、密度等性能指標,實時反饋材料性能的變化情況。根據這些反饋信息,對整個制備工藝進行動態優化。例如,當發現材料的電導率未達到預期值時,分析可能是氣泡去除不凈或各組分混合不均勻導致的,進而針對性地調整工藝參數,以提升燃料電池材料的性能。
通過以上對 V - MINI330 真空攪拌消泡混合器在真空環境設定、攪拌參數、溫度控制、混合順序以及在線監測與反饋等方面的工藝優化,能夠有效提升燃料電池材料的性能,為燃料電池的高效、穩定運行提供堅實的材料基礎。